Gear systems represent one of the most enduring and iconic forms of engineering, with their principles explored by some of history’s greatest minds, including Archimedes and Leonardo da Vinci. Due to extensive study, breakthroughs in gear technology are rare. Prominent gear technologies include Cycloidal drives (circa 1970), Strain Wave drives (circa 1950), and Planetary drives (dating back to around 100 BC). In this context, the Orbitless drive (patent pending) emerges as the first new low-ratio drive since the Planetary, offering several key advantages.
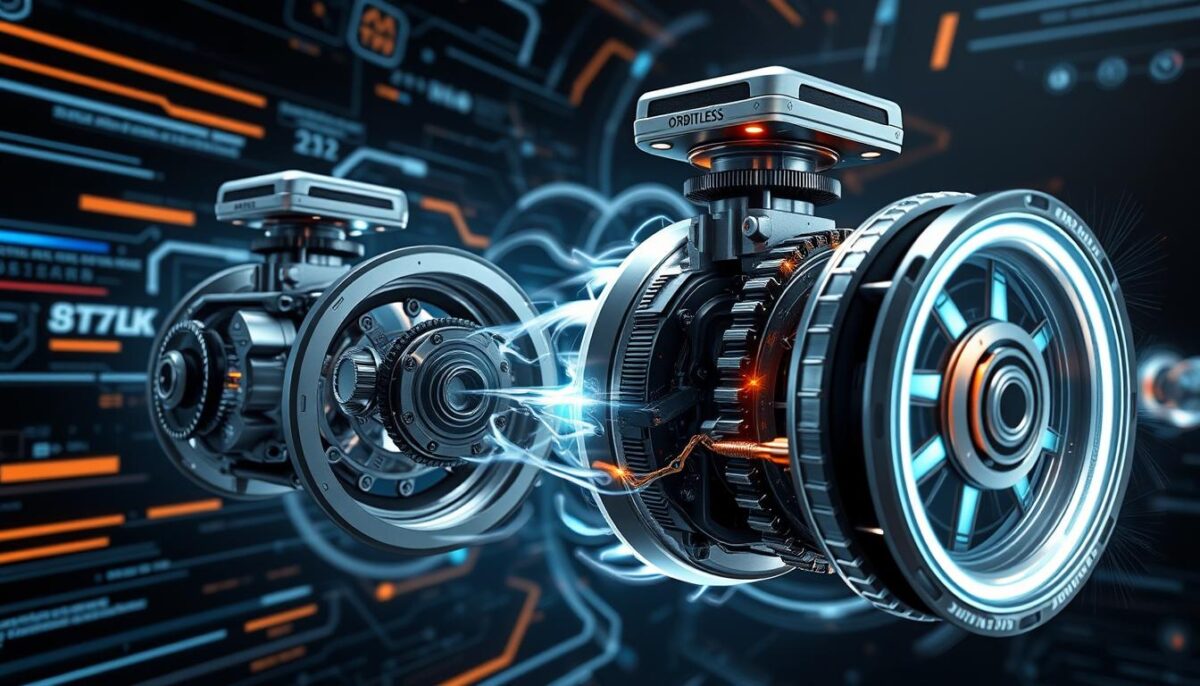
Key Features
While Orbitless drives share characteristics with Planetary drives—such as torque splitting and co-axial drive shafts that rotate in the same direction—they also boast benefits like reduced production costs and lower internal speeds. These factors contribute to significantly higher efficiency and extended bearing life.
Mechanical Similarities and Differences
Mechanically, Orbitless and Planetary drives share a similar architecture. Both consist of a sun gear (the input), planet gears, and a carrier (the output) that supports the planet gears via bearings. However, a critical distinction lies in the presence of a ring gear in Planetary drives, which is absent in Orbitless drives. Instead, the Orbitless design features a second carrier connected to the planet gears by an additional set of bearings. This configuration results in half as much tooth engagement and allows for a reduced gear ratio, catering to needs that traditional Planetary drives cannot satisfy—specifically, providing ratios as low as 1.5:1 compared to the practical minimum of approximately 3:1 for Planetary drives.
Cost Efficiency
All components found in an Orbitless drive also exist in a Planetary drive, but Orbitless drives avoid the most expensive and challenging part to manufacture: the ring gear. Ring gears are typically large, narrow, and feature internal teeth, necessitating specialized tools and processes for production. Their size requires substantial machinery or multiple sections for assembly, and their narrow design often deforms during heat treatment or manufacturing, especially when using soft materials like plastics. As a result, ring gears can be the most costly and least accurate components in a Planetary system, contributing to significant energy losses.
Adoption and Performance
Orbitless drives have gained traction with leading companies in high-precision actuators, such as Micromo-Faulhaber and Maxon Motor, each developing prototypes for distinct market segments. Comparative tests between Micromo’s Orbitless drive and traditional Planetary drives demonstrated energy loss reductions of 43% to 59%. In contrast, previous attempts to enhance efficiency through tooth geometry or other adjustments rarely exceeded a 1% improvement. The current prototypes, measuring less than 30mm, target sectors including robotics, medical technology, automotive, and aerospace. Importantly, the technology can be scaled for use in heavy machinery or energy generation without compromising its technical advantages.
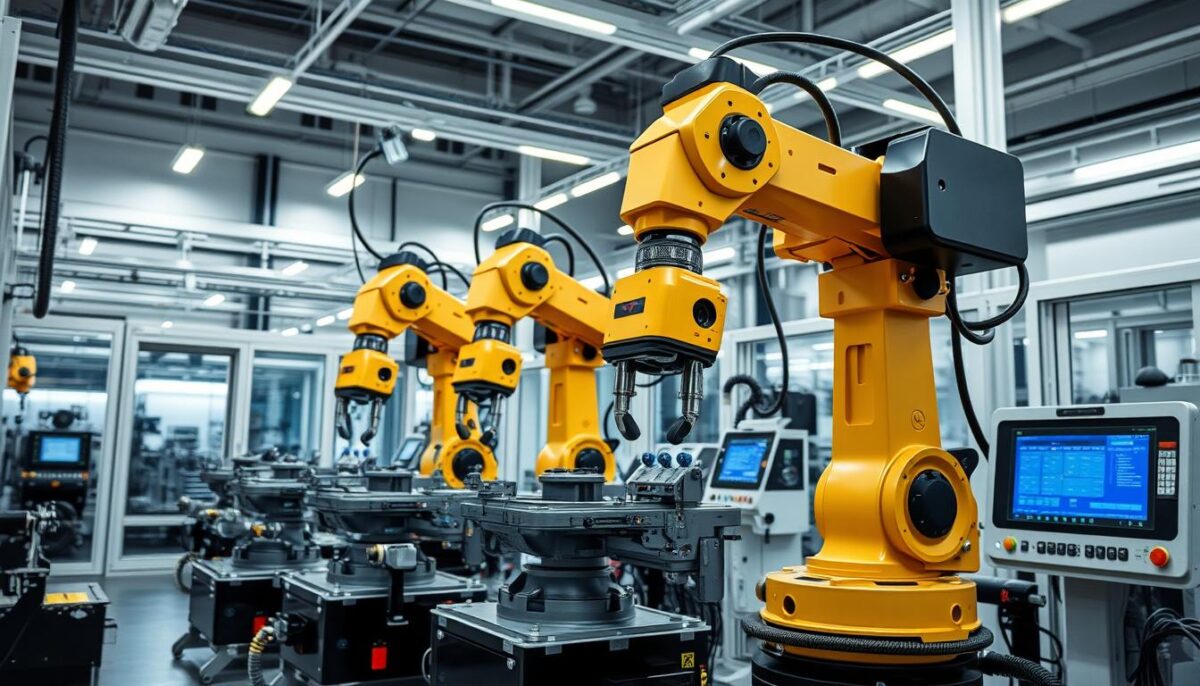
Advantages in Automation
In automated environments, friction can hinder controller stability, speed, and accuracy. The superior efficiency of the Orbitless drive is attributed to its ultra-low friction, translating to higher throughput and lower production costs. This efficiency leads to longer battery ranges for electric vehicles, more compact medical devices like infusion pumps for diabetes and cancer patients, and numerous other benefits across a wide array of motorized applications. Currently, two industrial partners are collaborating to develop an Orbitless drive tailored to meet these diverse needs.